What is a Quality Management System (QMS)?
In highly regulated industries like medical devices, ensuring product quality and regulatory compliance is non-negotiable. This is where a Quality Management System (QMS) becomes essential. But what exactly is a QMS? Is it a software tool, a process, or both? In this post, we’ll explore the meaning of QMS, its components, and why it’s critical for effective quality management.
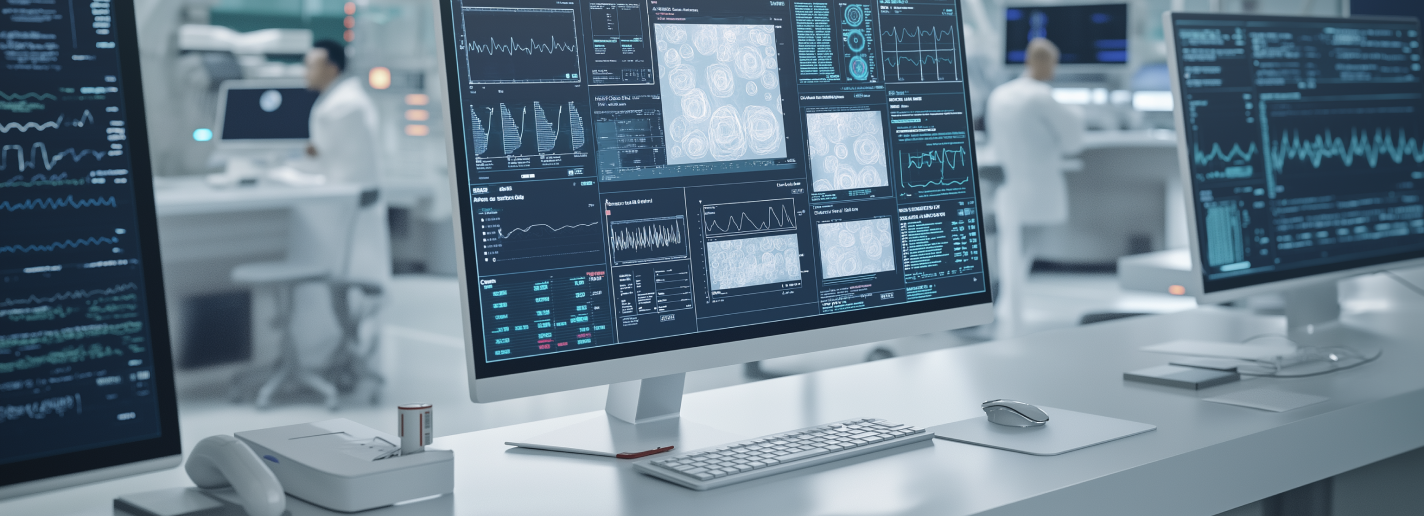
A QMS encompasses a framework of policies, processes, and procedures that guide organizations in delivering consistent, high-quality products while maintaining compliance with applicable regulations, such as ISO 13485 or FDA 21 CFR Part 11. Whether a company is developing a new medical device or managing post-market activities, a QMS ensures quality is at the forefront of every step.
Components of a Quality Management System
A robust QMS encompasses several key components that work together to ensure quality and compliance across all operations.
- Documents in a QMS: Documentation is the backbone of any QMS, covering everything from SOPs to manufacturing records. Proper document control ensures that records are accurate, up-to-date, and easily accessible during audits or inspections. This centralization reduces the risk of errors, fosters transparency, and simplifies compliance reporting.
- Training within a QMS: A QMS emphasizes continuous training to ensure employees understand their roles and stay up to date with the latest industry standards and internal procedures. Training records are maintained to demonstrate compliance during audits and improve workforce competency.
- Managing Events in a QMS: Quality events, such as non-conformances, deviations, and complaints, can disrupt operations if not managed effectively. QMS tools like CAPA help organizations track and resolve these events systematically, minimizing their impact on quality and compliance.
- Supplier Management in QMS: Suppliers play a vital role in product quality. A QMS provides a structured approach to evaluating, onboarding, and monitoring suppliers, ensuring they meet your company’s quality standards. This reduces the risk of subpar materials or components affecting the final product.
Practical Applications: How to Implement QA and QC in Your Operations
Implementing QA and QC effectively requires a structured and strategic approach tailored to your operations.
- Quality Assurance (QA): Start by developing comprehensive Standard Operating Procedures (SOPs) to establish a clear framework for processes. Ensure robust document control to track and manage records, which is essential for audits and regulatory reviews. Regular internal audits can identify gaps and improve compliance, providing a solid foundation for quality.
- Quality Control (QC): QC focuses on testing and validation to ensure product quality. Key methods include product sampling to evaluate batch consistency, statistical process control to monitor production variables, and equipment calibration to ensure tools and machines operate within specified tolerances.
For seamless implementation, Grand Avenue Software offers an industry-specific eQMS tailored to support both QA and QC. Whether you’re just getting started or optimizing existing processes, GAS and its trusted partners provide the tools and expertise needed to ensure compliance and operational excellence.
Importance & Advantages of a QMS
A QMS offers numerous advantages that extend beyond compliance, benefiting every aspect of a company’s operations.
- Lowering Operating Costs: By improving process efficiency and preventing costly quality issues, a QMS reduces the cost of poor quality. This includes minimizing waste, rework, and product recalls.
- Mitigating Operational Risks: A QMS helps organizations proactively identify and mitigate risks associated with non-compliance, such as regulatory penalties, legal challenges, and reputational damage.
- Boosting Revenue and Key Performance Indicators (KPIs): By consistently delivering high-quality products, companies can enhance customer satisfaction, reduce product returns, and boost KPIs like delivery times and retention rates.
- Strengthening Teams: A well-implemented QMS fosters collaboration by standardizing workflows, improving communication, and ensuring everyone works toward the same quality objectives. Employees are empowered to contribute to a culture of continuous improvement.
Who Can Benefit from Implementing a QMS?
While QMS systems are most commonly associated with large organizations, they are invaluable for companies of all sizes. Startups benefit from modular systems that can scale as they grow, while larger firms can streamline complex operations across multiple sites.
When is the Right Time to Implement a QMS?
While QMS systems are most commonly associated with large organizations, they are invaluable for companies of The right time to implement a QMS depends on the company’s size, industry, and regulatory environment.
For startups, implementing a QMS early ensures compliance from the start, reducing the likelihood of costly missteps during growth phases. Grand Avenue’s eQMS, for example, offers modular capabilities that allow startups to start small and expand as their needs evolve.
Established companies often implement QMS systems to replace manual processes or legacy tools that are no longer efficient. Advanced QMS features, such as multi-site document control and integration with CAPA systems, provide the scalability and efficiency these organizations need to manage complex operations.
Common Misconceptions about QMS
Despite its importance, several myths about QMS persist, often leading to misunderstandings about its role and benefits.
- Clarifying the Role of QMS in Regulatory Compliance: Many believe that implementing a QMS is optional, but for regulated industries like medical devices, it’s a mandatory requirement to meet global standards such as ISO 13485, FDA regulations, and the EU MDR.
- Dispelling the Myth that QMS is Solely for Quality Managers: While quality managers are key stakeholders, a QMS benefits every department, from production to customer service. By standardizing processes and improving communication, a QMS helps all teams align with organizational quality objectives.
- Overcoming the Belief That QMS is Too Complex for Small Companies: Modern QMS tools, like Grand Avenue Software’s eQMS, are designed with scalability in mind, allowing small companies to start simple and grow their systems over time.
What is a QMS Software and How Does it Work?
A modern QMS often includes software features that automate and streamline quality processes, making them more efficient and transparent.
- Document Control: QMS software ensures full document control by digitizing records, allowing for version control and quick access during audits.
- CAPA Management: It tracks CAPA processes, ensuring quality issues are addressed promptly and thoroughly.
- Real-Time Monitoring: QMS software provides dashboards and reports to monitor compliance and performance in real time.
- Integration Capabilities: Advanced systems integrate with other tools like ERP or PLM systems, ensuring seamless data flow across departments.
For med-tech companies, a QMS software like Grand Avenue’s ensures compliance with industry-specific standards while improving operational efficiency.
Conclusion
A Quality Management System is more than just a compliance tool—it’s a cornerstone of operational success. By integrating documents, training, CAPA, supplier management and other modules into a single framework, a QMS helps organizations maintain high-quality standards while streamlining operations.
For medical device companies, having a robust QMS is especially critical to ensure compliance and safeguard patient safety. Whether you’re managing documents, CAPAs, or supplier relationships, a QMS provides the structure and tools needed to excel.
To learn more about how a QMS can transform your operations, Request a Demo today.