How LSO Improved Efficiency and Audit Readiness with Grand Avenue Software
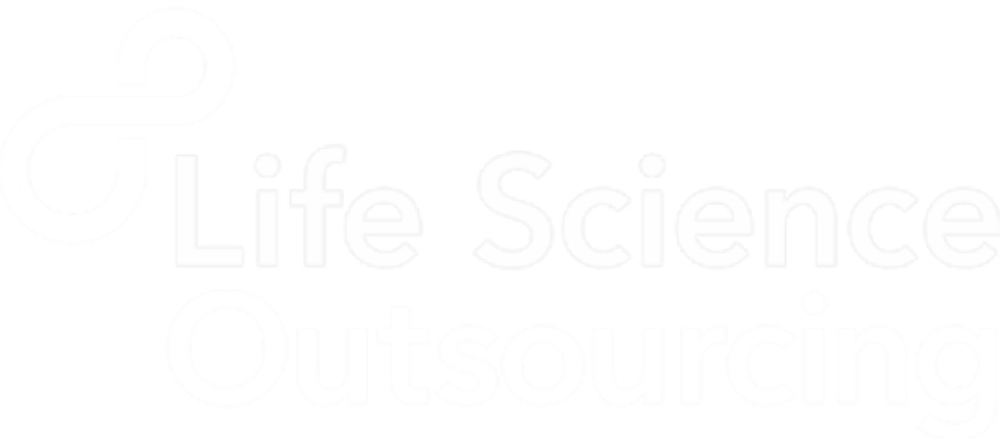
Overview
Client 4522_5c1e6c-7b> |
LSO (Life Science Outsourcing) 4522_11f6c5-32> |
Products 4522_9dd5aa-8c> |
Contract manufacturing services for dental implants, joint replacements, brain access systems, and other medical devices 4522_aeac71-c4> |
Challenge 4522_6b2aaa-5e> |
Ineffective tracking of equipment status and difficulty training employees without eQMS access 4522_dbea67-5a> |
Solution 4522_063baf-d5> |
Customized implementation of Grand Avenue Software’s eQMS to manage equipment tracking, document control, and quality events 4522_de1875-e5> |
Results 4522_089d29-5a> |
Faster product approvals, streamlined audits, and improved visibility across quality processes 4522_1dd9f5-65> |
Client: LSO (Life Science Outsourcing)
Products: Contract manufacturing services for dental implants, joint replacements, brain access systems, and other medical devices
Challenge: Ineffective tracking of equipment status and difficulty training employees without eQMS access
Solution: Customized implementation of Grand Avenue Software’s eQMS to manage equipment tracking, document control, and quality events
Results: Faster product approvals, streamlined audits, and improved visibility across quality processes
Client Intro: Contract Manufacturer Supporting Critical Medical Devices
LSO is a leading contract manufacturer serving the medical device industry, producing components for dental implants, joint replacements, brain access systems, and more. As a post-market organization working with a diverse range of devices, LSO operates under stringent quality and regulatory requirements.
To support continued growth and meet rising audit demands, LSO sought an electronic quality management system (eQMS) that could centralize processes, improve visibility, and reduce manual burden across its operations.
The Problem: Manual Workflows and Compliance Risks
Before implementing Grand Avenue Software, LSO’s quality team faced several operational challenges tied to an eQMS that no longer met their needs:
- Equipment Status Tracking: The team lacked an efficient way to monitor preventive maintenance (PM) and calibration (CAL) status, risking overdue or missed activities.
- Training Access: Employees without access to the quality system struggled to complete and verify required training, slowing onboarding and compliance.
- Audit Readiness: Quality documents were scattered across systems, complicating audit preparation and response.
- Approval Delays: Product document changes could take more than 30 days to approve, creating bottlenecks in product release and updates.
These inefficiencies introduced unnecessary risk, limited scalability, and consumed valuable time during audits and reviews.
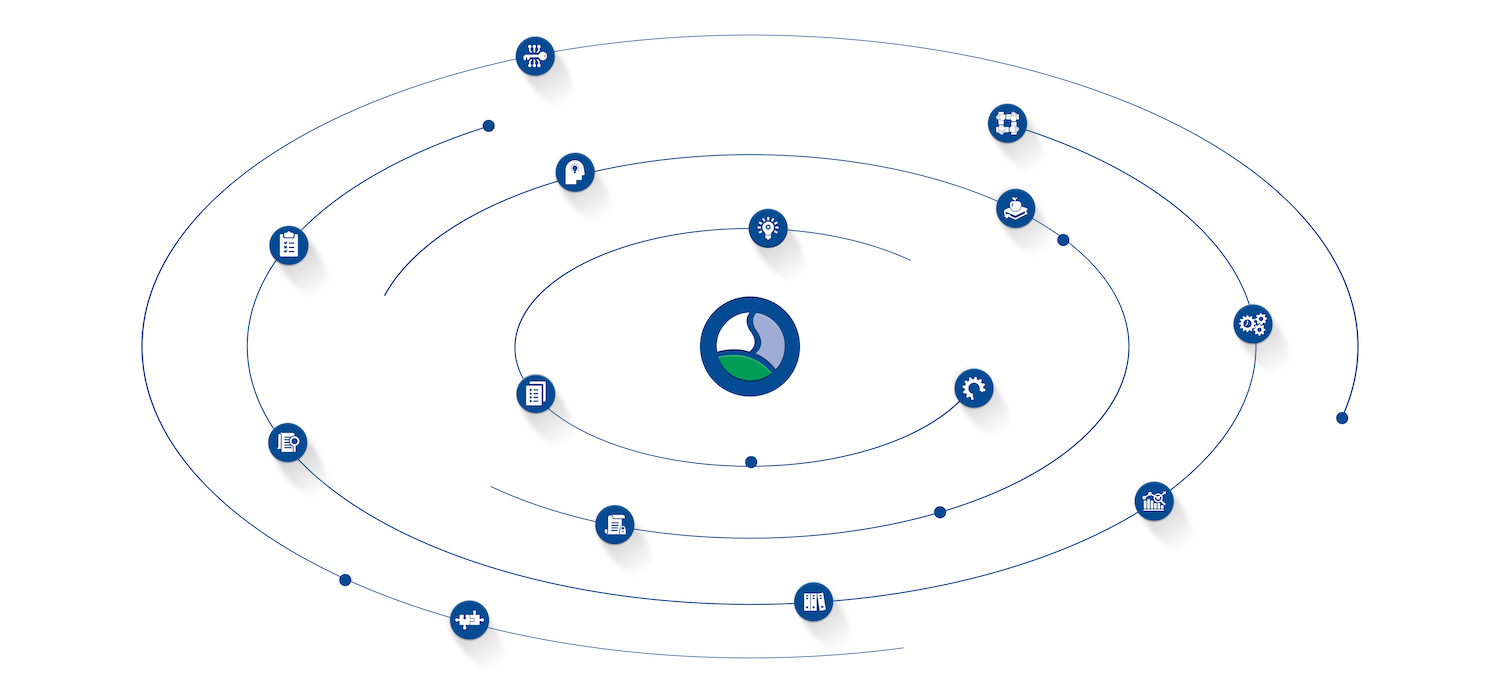
The Solution: Tailored Implementation of Grand Avenue Software
LSO selected Grand Avenue Software for its flexibility, intuitive design, and strong customer support. Key factors in the decision included:
- Customizable Configuration: LSO could easily adapt the system to meet their unique needs as a contract manufacturer.
- Responsive Support: Grand Avenue accommodated LSO’s condensed implementation timeline and provided expert guidance throughout the process.
- User-Friendly Setup: Despite their tight schedule, LSO was able to implement the system quickly thanks to the platform’s intuitive structure and dedicated customer support.
Implementation Approach
LSO’s implementation process focused on immediate impact areas:
- Equipment Management: Preventive maintenance and calibration tracking were digitized and made easily accessible to the appropriate personnel.
- Document Control: All quality documents were centralized, allowing instant access during audits and simplifying day-to-day management.
- Quality Event Visibility: Custom workflows allowed LSO to clearly track the status of CAPAs, complaints, and nonconformances through visual flow diagrams.
With dedicated support from the Grand Avenue team, LSO transitioned quickly from their previous eQMS—completing configuration, validation, and go-live on an accelerated timeline.
“The level of support was excellent and Grand Avenue was able to accommodate our condensed implementation timeline.”
— Andrew Ureno, LSO
The Results: Faster Approvals and Streamlined Audits
LSO achieved immediate, measurable benefits with Grand Avenue Software:
- Faster Document Approvals: DCR approval times were cut in half—from at times more than 30 days to around 14 days.
- Streamlined Audits: Audit preparation became far easier, with all quality documents accessible in just a few clicks.
- Improved Equipment Oversight: Equipment PM and calibration statuses are now fully trackable, reducing risks and improving compliance.
- Better Process Visibility: Teams can now instantly see the status of quality events, improving oversight and reducing delays.
Conclusion: A System Built for Speed, Flexibility, and Growth
By implementing Grand Avenue Software, LSO modernized its quality management processes without overcomplicating workflows. The combination of rapid setup, easy customization, and reliable support made it possible for LSO to quickly gain efficiency and reduce risk.
With a strong foundation now in place, LSO is equipped to continue scaling its operations and refining processes, knowing that their quality management system can grow alongside their business needs.