What is Total Quality Management (TQM)?
Total Quality Management (TQM) was once a leading philosophy in quality management, emphasizing continuous improvement, employee involvement, and customer satisfaction. During the 1980s and early 1990s, TQM gained widespread adoption, particularly in manufacturing and service industries, helping organizations reduce defects, improve efficiency, and optimize workflows.
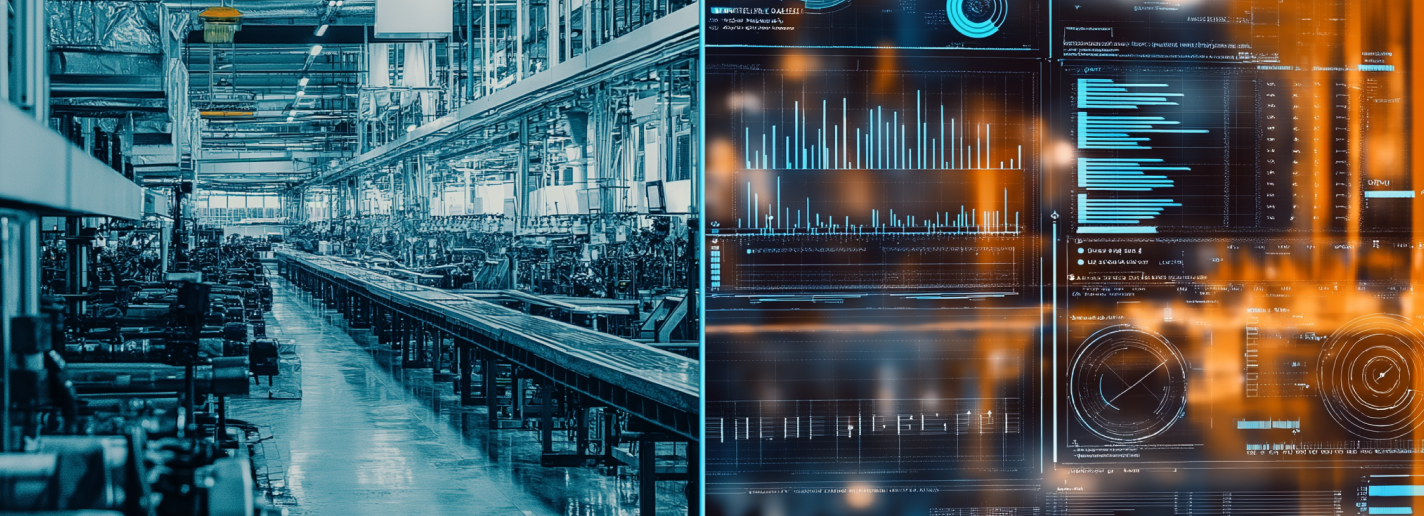
However, as quality management systems (QMS) and international standards such as ISO 9001 and ISO 13485 evolved, TQM as a standalone methodology became less prevalent. Today, many of its principles live on in modern quality frameworks, including ISO standards, Six Sigma, Lean Manufacturing, and national quality award programs like the Deming Prize and the Malcolm Baldrige National Quality Award.
This guide explores TQM’s core principles, its historical significance, and how its philosophy continues to influence today’s quality management practices.
Defining Total Quality Management and Its Core Principles
TQM was designed as a broad, organization-wide approach to improving quality through cultural and process changes. It encouraged companies to move beyond isolated quality control measures and instead integrate quality improvement at every level of an organization.
Although TQM as a formal methodology has largely been replaced by structured QMS frameworks, its foundational principles remain relevant:
- Customer Focus – Organizations should prioritize customer needs and satisfaction when designing processes.
- Continuous Improvement – Quality should evolve over time, using iterative refinements to enhance processes.
- Employee Involvement – Everyone, from executives to frontline staff, plays a role in maintaining and improving quality.
- Process-Oriented Thinking – Quality should be built into the entire production and service lifecycle, not just inspected at the end.
- Data-Driven Decision Making – Performance metrics and real-time analytics should guide process improvements.
These core principles continue to influence modern quality systems that integrate compliance, efficiency, and innovation.
Historical Context and Evolution of TQM in Organizational Settings
TQM originated in the mid-20th century, heavily influenced by quality pioneers like W. Edwards Deming and Joseph Juran, who promoted systematic approaches to process improvement.
During the 1950s and 1960s, TQM gained prominence in Japan, where companies like Toyota and Sony adopted it to enhance production efficiency. By the 1980s and early 1990s, TQM spread to the United States and Europe, becoming a key driver of corporate quality programs.
However, as formalized quality management standards like ISO 9001 and ISO 13485 were developed, TQM lost favor as a standalone methodology. Many of its principles were incorporated into:
- ISO 9000 series – A structured, certifiable framework for quality management.
- Industry-specific QMS standards – Such as ISO 13485 for medical devices, which ensures compliance with regulatory requirements.
- Lean, Six Sigma, and other process improvement methodologies – Which refined TQM’s focus on efficiency and defect reduction.
Although interest in TQM declined after the mid-1990s, its philosophy continues to influence quality-focused initiatives across industries.
TQM vs. QMS: Key Differences
While TQM and QMS both focus on improving quality, they differ in approach and structure.
- TQM is a philosophical approach that fosters a company-wide culture of continuous improvement, employee engagement, and customer satisfaction. It encourages organizations to embed quality at every level but lacks formalized guidelines for implementation.
- QMS is a structured framework with documented procedures, compliance requirements, and regulatory oversight. Standards like ISO 9001 and ISO 13485 establish clear guidelines for audits, certification, and quality assurance.
Continuous Improvement vs. Compliance
- TQM emphasizes ongoing refinement through internal initiatives and feedback.
- QMS ensures organizations meet regulatory benchmarks and audit requirements for compliance.
Today, many companies integrate TQM principles within a QMS framework, using data-driven decision-making and structured processes to achieve both operational excellence and regulatory compliance.
Implementing TQM and QMS in Organizations
Rather than treating TQM and QMS as competing frameworks, many organizations today blend TQM principles with a structured QMS to achieve both continuous improvement and regulatory compliance.
Integrating TQM Principles within a QMS Framework
Successful organizations still apply TQM principles in a modern QMS structure by:
- Encouraging employee-driven quality improvements within a compliant framework.
- Incorporating real-time performance analytics to track quality enhancements.
- Using structured feedback loops for ongoing process optimization.
Customer Focus and Satisfaction in TQM
TQM emphasized long-term customer trust through:
- Proactive customer feedback collection to shape improvements.
- Strengthening customer relationships with consistent product quality.
- Responsive quality adjustments based on market needs.
Employee Involvement and Continuous Improvement
Employee engagement remains a critical factor in modern quality initiatives. Organizations can apply TQM’s employee-centric approach by:
- Providing training programs on quality improvement.
- Encouraging cross-functional collaboration to address quality challenges.
- Rewarding innovative contributions that improve efficiency.
Data-Driven Decision Making and Process Improvement
TQM promoted data analysis as a tool for process refinement. Today, companies use:
- Real-time analytics to track defect rates, efficiency, and compliance trends.
- Digital QMS platforms to automate data collection and corrective actions.
- Continuous monitoring tools to detect and prevent quality issues proactively.
Final Thoughts: TQM’s Influence on Modern Quality Management
TQM was a pioneering movement that laid the groundwork for modern quality management systems, regulatory frameworks, and process improvement methodologies. While TQM as a formal approach has largely been replaced by ISO 9001, ISO 13485, and Lean Six Sigma, its core principles remain deeply embedded in today’s quality initiatives.
For companies looking to blend continuous improvement with regulatory compliance, Grand Avenue Software offers QMS solutions designed to align with modern quality standards while retaining the flexibility of TQM-inspired best practices.
Explore our Solution Suite or Request a Demo today to strengthen your quality management strategy.