Medical Device Quality Control Plans:
The Basics
For medical device companies, quality control is not just about maintaining high product standards—it’s a regulatory necessity. A medical device quality plan ensures that all processes, from design to post-market surveillance, align with industry regulations while consistently delivering safe, reliable products.
In this post, we’ll break down the essential components of an effective medical device quality control plan, explore best practices for monitoring quality outputs, and highlight continuous improvement strategies that drive compliance and operational excellence.
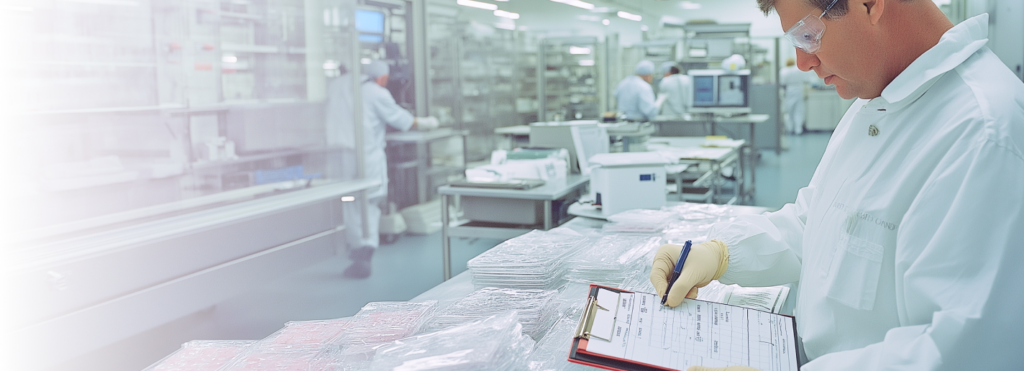
The Basics: What is a Medical Device Quality Plan?
A medical device quality plan is a structured framework that defines how a company maintains and monitors product quality throughout the lifecycle of a device. It incorporates risk-based decision-making, regulatory compliance, and continuous monitoring to ensure product consistency and safety.
Defining the Role and Purpose
A well-designed quality plan serves as a roadmap for aligning manufacturing, supplier management, document control, and regulatory compliance. It ensures that all teams—from R&D to production—adhere to documented quality protocols.
Importance of Quality Plans in Ensuring Compliance and Product Quality
Regulatory bodies like the FDA (21 CFR Part 820) and ISO 13485 mandate stringent quality control measures for medical device companies. A comprehensive quality plan not only ensures compliance but also enhances efficiency, minimizes defects, and strengthens trust with customers and regulatory agencies.
Key Components of a Medical Device Quality Plan
A quality control plan should be built around core elements that guarantee compliance and product integrity.
Responsibilities and Roles
Clearly defining who is responsible for quality assurance is critical.
- Quality Managers oversee compliance with regulatory requirements.
- Production Teams ensure that manufacturing meets established quality criteria.
- Regulatory Affairs Professionals align processes with global medical device standards.
Setting Quality Objectives for Medical Device Manufacturers
Every quality plan should include measurable quality objectives, such as:
- Reducing non-conformances and defects.
- Improving supplier performance metrics through supplier management.
- Maintaining 100% compliance with internal and external audits.
By setting clear goals, companies can track progress and continuously refine their processes.
Identifying Inputs and Key Elements for the Quality Plan
Quality control starts with defining inputs—the raw materials, components, and processes that contribute to the final product.
Ensuring Production Consistency and Quality Assurance
- Establish strict supplier quality requirements to reduce variability.
- Utilize incoming material inspections to detect defects early.
- Implement CAPA procedures to prevent recurring issues.
Proactive supplier and production oversight reduces errors, lowers costs, and prevents compliance failures.
Monitoring and Evaluating Outputs to Ensure Compliance
The output of a medical device quality plan is a consistent, compliant product. Monitoring these outputs involves:
- In-process inspections at various manufacturing stages.
- Finished device testing to verify adherence to specifications.
- Post-market surveillance to track product performance and customer complaints.
Regulatory bodies require detailed quality documentation for every stage of production. Using an advanced document control system helps maintain accuracy and audit readiness.
Documentation of Standards and Procedures
A robust documented quality plan ensures transparency and regulatory compliance. This includes:
- Standard Operating Procedures (SOPs) to define best practices.
- Work Instructions that guide production staff.
- Deviation and Non-Conformance Reports for tracking issues and corrective actions.
Proper documentation not only supports FDA and ISO audits but also helps streamline quality improvement initiatives.
Evaluating Customer Satisfaction and Feedback
Customer feedback is a key quality metric. Medical device manufacturers should:
- Track customer complaints and returns through a structured complaint handling system.
- Conduct post-market studies to assess long-term device performance.
- Use customer surveys to gauge satisfaction and identify areas for improvement.
A strong feedback loop helps refine manufacturing processes and ensures continued regulatory compliance.
Continuous Improvement Strategies
Quality control is not a one-time effort—it’s an ongoing process. Companies should implement:
- Regular internal audits to identify process inefficiencies.
- Data-driven decision-making, using analytics to detect quality trends.
- Lean manufacturing principles to eliminate waste and improve efficiency.
By fostering a culture of continuous improvement, companies can proactively address potential risks and enhance overall product quality.
Overview of Quality Plan Essentials for Company-Wide Approval
A medical device quality plan must be approved and implemented across all departments. To ensure seamless execution:
- Involve leadership in defining quality priorities.
- Train employees on regulatory requirements and quality objectives.
- Utilize QMS software to integrate processes and track compliance metrics.
Having an organization-wide commitment to quality ensures that medical devices meet the highest safety and performance standards.
Final Thoughts: Building a Strong Medical Device Quality Plan
An effective medical device quality control plan is the backbone of compliance and product reliability. By implementing robust monitoring, clear documentation, and continuous improvement strategies, companies can safeguard patient safety while meeting regulatory demands.
For manufacturers looking to streamline quality management, explore Grand Avenue Software’s Solution Suite or Request a Demo today.