Quality Assurance vs. Quality Control Explained
Ensuring high-quality products is essential in any industry, but especially in the regulated field of medical devices, where patient safety and regulatory compliance are critical. Quality Assurance (QA) and Quality Control (QC) are two critical components of a robust quality management system (QMS), each serving distinct roles. This post will clarify the differences between QA and QC, highlight their practical applications, and provide insights into how med-tech companies can integrate both approaches effectively.
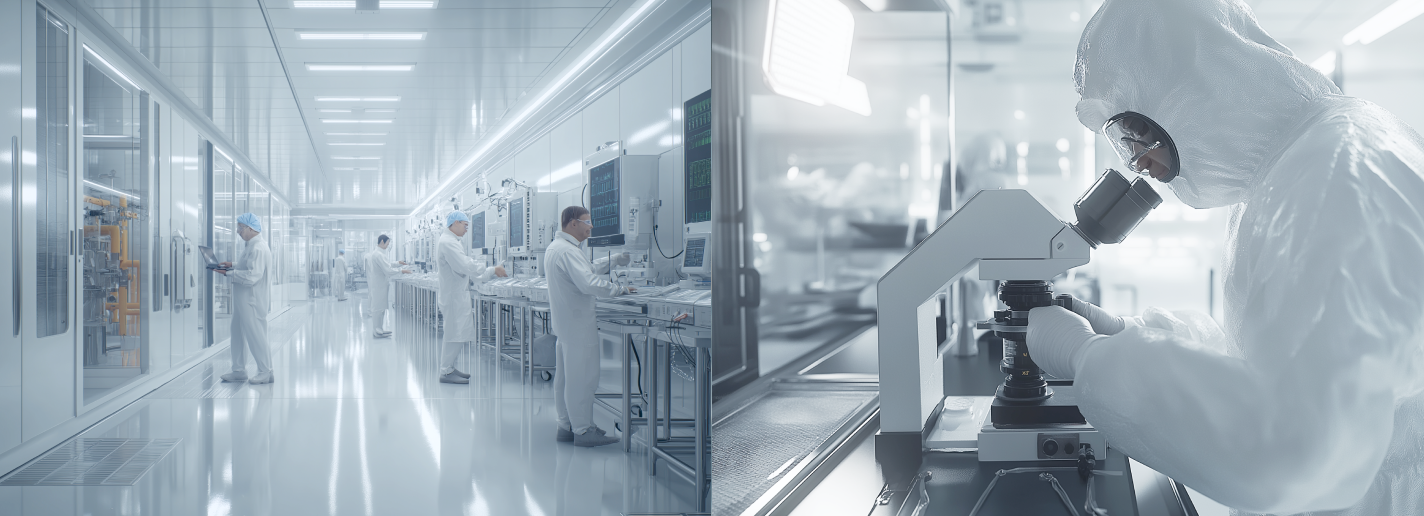
QA vs. QC: Key Differences and Applications
At their core, Quality Assurance and Quality Control aim to achieve the same goal—ensuring product quality. However, their methods, objectives, and roles within a company differ significantly.
- Quality Assurance (QA): QA focuses on preventing defects by creating and managing systems, policies, and processes that ensure quality throughout the production lifecycle. Key QA activities include establishing effective workflows, maintaining document control, and training employees to follow regulatory guidelines like ISO 13485 and FDA 21 CFR Part 11. QA is proactive, focusing on building quality into every stage of production.
- Quality Control (QC): QC, by contrast, involves identifying defects in finished products through inspections, testing, and validation. QC ensures the final product meets defined quality standards, protecting end users and maintaining regulatory compliance. Unlike QA, QC is reactive, focusing on detecting and correcting issues before the product reaches the customer.
Practical Applications: How to Implement QA and QC in Your Operations
Implementing QA and QC effectively requires a structured and strategic approach tailored to your operations.
- Quality Assurance (QA): Start by developing comprehensive Standard Operating Procedures (SOPs) to establish a clear framework for processes. Ensure robust document control to track and manage records, which is essential for audits and regulatory reviews. Regular internal audits can identify gaps and improve compliance, providing a solid foundation for quality.
- Quality Control (QC): QC focuses on testing and validation to ensure product quality. Key methods include product sampling to evaluate batch consistency, statistical process control to monitor production variables, and equipment calibration to ensure tools and machines operate within specified tolerances.
For seamless implementation, Grand Avenue Software offers an industry-specific eQMS tailored to support both QA and QC. Whether you’re just getting started or optimizing existing processes, GAS and its trusted partners provide the tools and expertise needed to ensure compliance and operational excellence.
Benefits of Integrating QA and QC: Enhancing Quality Management Practices
By integrating QA and QC, companies can achieve a comprehensive quality management strategy. Key benefits include:
- Improved compliance: QA ensures processes meet regulatory requirements, while QC provides tangible evidence of compliance through testing and validation.
- Reduced risks: Proactive QA practices prevent defects, and QC detects any remaining issues before products reach the market, minimizing the risk of recalls or legal challenges.
- Cost savings: Early identification of potential problems through QA and QC reduces rework, delays, and costly corrective actions.
Choosing the Right Approach: Tailoring QA and QC Strategies to Your Operation
Medical device companies face unique challenges, from stringent regulations to the need for precise documentation. Tailoring QA and QC strategies to your specific needs is critical:
- Startups: Modular eQMS solutions like Grand Avenue’s allow startups to implement essential QA and QC processes such as document control and CAPA systems, then scale them as their operations grow.
- Established companies: Larger firms may benefit from more advanced features such as risk management, equipment management, and training management.
A flexible, scalable QMS like Grand Avenue Software helps organizations implement tailored QA and QC processes, ensuring consistent quality and compliance at every stage.
Conclusion
While QA and QC have distinct roles, their integration is vital for achieving and maintaining high-quality products. Med-tech companies can streamline these processes with tools like Grand Avenue’s eQMS, ensuring compliance and efficiency.
For more information on improving your quality management practices, Get a Demo today.